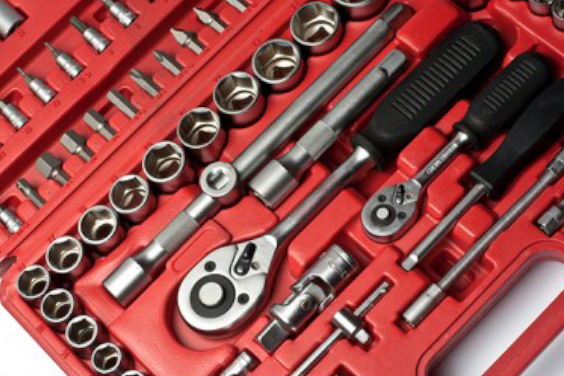
As of the first quarter of 2021, the market size value of injection molding was $284.7 billion. That sheer number is all the proof you need to know how massive injection molding has become integral in the manufacturing economies around the world. With plastic products forming most of the daily-use items, it is not a surprise that injection molding continues to grow every year. But what exactly are these products that are made using this process? How and where are they used?
We are going to explore these questions and more. We will take a deep dive into the world of injection molding, look at the raw materials used, the CNC machinery and the technologies involved as well as the challenges facing the industry and how it will shape itself for the future. If you have always been curious to know about injection molding and what it really entails, then stick around to the end.
People use plastic products at every turn in their daily lives. Be it in packaging their food or the tools they use, one way or another, they have to rely on plastic products. Injection molding is the easiest way to turn any plastic material into a usable object, and the following are the most common products you are most likely to come across today.
Source: Pixabay
Plastic bottles make up the bulk of all plastic products in use today. From packaging water to soft drinks and chemicals, among other things. They are the most manufactured injection molding products that can be found in every retail shop and beyond. Plastic bottles are the easiest to make, and getting the raw materials needed for their manufacturer is also quite easy. This is the reason why they are made in such huge numbers.
Source: Pixabay
Source: Pixabay
Source: Pixabay
Electrical components require ample insulation to make them safe for use around the house and workplaces. The best way to do this would be to create housing that fits them the right way before being sold to consumers. Injection molding is the best and the fastest way to get electrical housings of any shape and size in large numbers. Some electrical components that require plastic housing include TV remotes, computers, TVs, among many others.
Source: Pixabay
No other products have benefited greatly from injection molding than toys. Unlike other items, they don’t require complex construction; they simply have to attain certain shapes and be lightweight at the same time. Injection molding is the only way to make toys of all kinds and shapes at very rapid paces. Another advantage of making toys using injection molding is the safety aspect. The parts are made whole without any small splinters, and this is ideal for babies as it reduces the risk of toy parts getting swallowed by accident.
Source: Pixabay
Source: Pixabay
Source: Pixabay
Some hardy tools can be fashioned out of plastic for use in the agriculture sector with ease. The advantage of switching to plastic molded tools is that they are durable, can withstand extreme temperatures, and are way much cheaper to make compared to other materials. Many farmers around the world are using plastic tools and equipment for most of their small tasks around their farms that don’t require heavy machinery.
Source: Pixabay
The range of household goods that are made using injection molding cannot fit here. Anything you can think of can be reproduced to the exact measurements using injection molding. From utensils, flower pots, wire ties, air freshener units, to plastic chairs, to other types of furniture, decor, containers, and so many more. Since people spend more time in their houses, many injection molding companies have specialized in the creation of household goods only due to the high demand that’s ever-increasingevery dayy.
Source: Pixabay
Source: Pixabay
Source: Pixabay
A huge part of vehicles is made using plastic injection molds. Not every part of the car is made using metal, as that would add unnecessary weight. To counter that, there are parts like the dashboard, radio controls, cup holders, seats, increasing every day a lot of other elements that are made using plastic and injection molding is the best way of getting the right shapes. The same applies to heavy machines. They have parts that are not involved in the heavy lifting that is made using solid plastic injection molds. The advantage of using molds for all these parts is that they are easy to replace, and they help bring down the overall weight of cars and machines.
Source: Pixabay
The medical sector is another area that makes use of injection molding to fashion out all kinds of products that are vital in saving the lives of patients. Things like syringes and drug containers have to be made using plastic as they are cheaper and safer compared to other materials. They can also be manufactured in bulk, meaning that there’s a constant flow of supplies that far outstrips the pace of their use.
This has become very evident in the last 12 months the pandemic caused many hospitals to be over capacity. Injection molding is also preferred in making medical tools as there’s more flexibility when it comes to product design. You can create any size and shape of medical tool as you deem fit, depending on the type of molding machine at your disposal. Some common products include disposal bins, wall mounts, medication trays, among many others.
Source: Pixabay
Source: Unsplash
Source: Unsplash
There are a lot of clear plastic products made through injection molding that is used to store and package food at all levels. Perishable foods and drinks are naturally stored in airtight plastic bottles and containers to increase their shelf lives. Besides packaging, there are also a lot of products used for food preparation that is made using injection molding; this includes high-temperature serving pans, bread trays, NSF food service products, among many others.
Source: Unsplash
The use of some types of plastic materials as an alternative for construction has been ongoing for years now, and it’s getting better and better, thanks to injection molding. Parts like roofing, roofing vents, and deck fasteners can be made cheaply and after using plastic materials, and this can bring down the cost of construction significantly without impacting the structural integrity in any way. The other advantage is the choice of colors that one can choose from since plastic can be molded in any shape, design, and color depending on the personal preferences of the client.
Source: Unsplash
Source: Unsplash
To understand how plastic molding products are made, it is vital that you know the type of raw materials that go into their construction, as that will give you a clear picture of how they are used—some of the most common raw materials used in the making include the following.
Nylon: Also called Polyamide, nylon is the most commonly used raw material in injection molding as it is widely available and easy to extract from petroleum-based products. It is malleable with low melting temperatures, and this makes it the perfect material to use for all kinds of uniquely shaped products. Nylon can be used to make strong and solid mechanical parts like gears and bushings for automotive parts as they are able to counter wear and tear as well as chemical resistance.
Acrylic: Acrylic is used for products that are transparent, and for this reason, you will find it in transparent walls, lighting equipment, among many others. Acrylics are a very good alternative for glass as it is stronger, meaning it cannot be shattered by any kind of force. It is also quicker and cheaper to make, and the color options are so many. It is also scratch-resistant and can withstand any type of weather without sustaining any damage. Another advantage of acrylic is that it doesn’t contain the toxic chemical called Bisphenol A, which is responsible for food poisoning. This is the reason why acrylic is best suited for food containers.
Polycarbonate: Polycarbonate is the material you see on compact discs with a shiny and colorful surface. This is the material you go for when you want something that’s stronger than acrylic. It has a predictable form, and this gives people a precise dimensional control that can be maintained all through the injection molding process. However, it is not suitable for food storage or for making closed containers as it is too brittle.
Polyoxymethylene: This is a special type of acetal resin that is primarily used for making mechanical and automotive parts that would, in most cases, require metallic parts. This type of plastic raw material is very strong, tough, and rigid and, when made in the right design, can be used as movable parts in a car for a very long time without affecting the performance of the structural integrity. Polyoxymethylene is used in the making of gears, knife handles, fasteners, ball bearings, among many other parts
Polystyrene: Polystyrene is the material used to make hard and durable toolboxes and other containers for power tools. It is one of the hardest forms of plastic and is a very reliable material when it comes to making hardy containers. The other advantage is the cost of making them; despite their hardiness, it costs way less to make them compared to other types of plastic materials. The only drawback is that they are very bad for the environment.
Acrylonitrile Butadiene Styrene: Also called ABS, this is an opaque thermoplastic polymer that is tough, with good dimensional stability, high resistance, with good anti-breaking and tearing attributes. The material also has a very low melting temperature, and this makes it ideal for quick changes. The material is mostly used to make casings and insulation for electronic parts like phone adapters, socket guards, and keyboard keys.
Polypropylene: This is another thermoplastic material that is used in making food storage containers. It is widely used in the packaging industry as it is not toxic and doesn’t let any chemicals from outside sip into the content of the package. It can also be subjected to extreme conditions like hot water without getting degraded. It also has a very high tolerance for chemicals and moisture with one of the most incredible elasticities, impacts strength and toughness.
Thermoplastic Polyurethane: This is a soft and elastic type of plastic that is used for things like phone and laptop cases. It is soft, elastics, and has great tensile strength. It is mixed in with rubber, and this is where it gets its rubbery and elastic properties. It performs very well in extreme temperatures and is a good material for making power tools, sporting goods, and cable insulations.
Thermoplastic Rubber: This is a mix of rubber and plastics, and they are used for making medical tools like catheters, suspension bushings, headphone cables, among many others. It is one of the easiest materials to use in injection molding due to its low melting temperatures. They have an outstanding tolerance against extreme weather conditions, heat, and chemicals, and the great impact strength they have makes them one of the most durable injection molding materials you will ever come across.
Source: Unsplash
Despite the great success it has enjoyed over the years and the continued growth in manufacturing, injection molding is not without some challenges. The following are the most notable ones so far.
Pollution: The one thing plastic has never been able to fully address is pollution. It takes very long for plastic to degrade, and in some cases that never happens. The first plastic material ever made is still intact to this day. There are efforts to find alternative plastics, but so far, nothing has been found that’s as efficient as plastic.
Demand: The demand for plastic products, deposit the ravaging effects on the environment, is at an all-time high, and this has made meeting the demand a challenge for many injection molding manufacturers. The cost of upscaling has been too much for many companies, and this deficit has led to a lot of problems in the industry as a whole.
Skill Gaps: As automation takes over, the most valuable skill sets among experts are rapidly going down, and soon, there will not be anyone left with the knowledge of designing unique products in injection molding. The cost of training new people is also high for many companies and turning to automation is ultimately the only option left for many of them.
Cost of Automation: Automation is the future and the only way that most injection molding companies will be able to keep up with the rising demand is by switching to industrial robots for their operations. The stumbling block, how warm is that the cost of setting this up is too huge even for the most established brands. Production will have to take a significant hit for any form of automation to be pulled off.
We cannot do without plastic, at least not yet, and that’s the stark reality facing the world right now. The best that we can do is to find more sustainable ways of deadlines with what has already been released into the ecosystem, but that too will take time. If you wish to know more about plastic injection, the behind-the-scenes process, and the things that can be made from it, check out our website when you have the time and have all your questions answered by our team of experts.
+86-755-8524 1121
marketing@rydtooling.com
No. 2, HongKan 1st Road, YanChuan Community, YanLuo Street, BaoAn District, ShenZhen City, China. Post Code 518105.
Subscribe to our newsletter to get manufacturing news and updates!