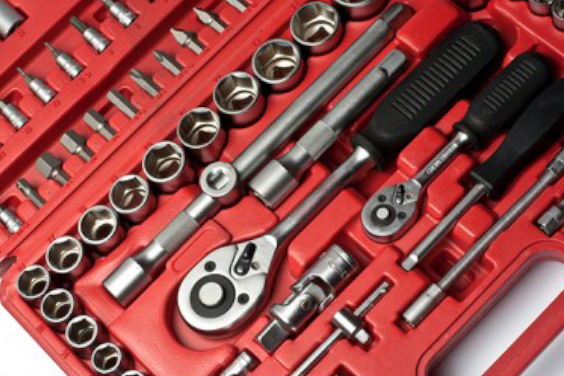
Insert Molding Process Step by Step
It is dangerous to make use of components after they’ve been manufactured without encasing them with plastic. It’s essential to encase these components to make
Share
Share
The sprue can be described as a component of the runner that allows molten plastic to be infused into the mold via the nozzle of an injection machine. A fastener sprue bush is a sprue that is secured with two bolts, which also works to prevent sprue disassociation associated with high injection pressure.
This article aims to inform you on injection molding sprue detailing what it is, the various types of injection mold sprue, and a sprue bush design. Read on to find out more.
Source: Pinterest
Sprue bushing injection molding connects the nozzle of the injection machine to the injection molding. That’s the same component of the runner that makes it possible for the molten plastic material to be infused into the mold via an injection machine’s hose. Sprues, runners, and gates transport the plastic’s molten material from the injection unit’s hose to the specific cavities.
Since these plastic materials can be repurposed in the shape of regrind, their presence limits the effectiveness of the injection molding machine because they must be plasticized in the cylinder. With smaller parts, they could account for half or upwards of the shot poundage.
The sprue can be regarded as the direct consequence of the mold to the hose of the injection machine. Singular molds where the sprue relates to the molded part have been shown to have direct sprue gating. The cooling time of this sprue is frequently used to determine the capacity of a specific injection mold.
In addition to offering adequate cooling of its sprue bushing, the circumference of the smallest opening in the sprue bushing must be kept as short as possible and allowed by proper filling of the cavity. There are no broadly applicable rules here because filling the cavity is dependent on a variety of factors.
A 1.5° draft should be present on the sprue. A higher draft may facilitate extraction from the sprue bushing, but it is a function of the runner’s length, as it is anticipated that the pressure drop in a runner improves at least proportionately with length.
It will almost certainly rise more than proportionately since the cross-section is decreased by solidification of the melt along its walls, and the higher the reduction, the larger the distance from the sprue. Since the sprue and runner systems indicate the lost materials and plasticating capacity, the runners should be as short as feasible and with the shortest cross-section possible.
Source: Pinterest
Cold sprue bushings are embedded into the mold to create a channel here between the injector of the molding machine and the mold cavity. If aesthetic is important, they are unheated and end up leaving a sprue which must be excluded, often by a secondary operation. On the hose end of the bushing, there are two critical dimensions: the “O” dimension hole entrance and the circular radius.
Hot sprue bushings are put into the mold to create a hot passage in between molding equipment nozzles and the mold chamber. A heat exchanger housed inside the brushing is utilized to maintain the resin melt hot inside the brushing.
Source: Pinterest
Sprue bushings normally have a circular radius of half or 3 quarters of an inch, but flat-type brushings with a flat surface rather than a nozzle radius are also available. Buyers must also choose several other dimensions.
Sprue bush can be designed based on your calculations or purchased from another provider. Sprue with two bolts is used for small molds, and it can be used with injection machines weighing less than 350 tons. Sprue with four bolts is used for large molds, and it may be used with injection machines weighing more than 200 tons.
When designing or selecting a sprue bush, keep in mind that the sprue’s ball radius must be greater than the radius of the nozzle. If it is less than the diameter of the nozzle, there will be a space between both the sprue and the nozzle, the resin will overflow, and the injection machine’s tension will be lost.
The inner hole diameter must be greater than the nozzle hole diameter. If it is less than the nozzle’s hole diameter, it will prohibit the molten plastic material from moving. The nozzle’s diameter is normally around 25mm. When you select the sprue, make a note to check the injection machine catalog and make sure it is more than 0.5 m or larger.
The inner hole angle is normally around 26 degrees. You should aim for a 35-degree angle for the greatest results. Check the dimensions of the mold plate; the length of the sprue must correspond to the thickness of the plate. If indeed the sprue thickness is big, the sprue bush may need to be cooled to shorten the turnaround time of the injection process.
The sprue and runner system is the connection that links the equipment tip to the chambers. During the injection step of the molding cycle, molten material travels via the sprue and runner to the cavities. If you want to know more about it or want to be a molding manufacturer, it is advisable that you consult with a plastic injection molding OEM just to get the best services and equipment available in the market.
It is dangerous to make use of components after they’ve been manufactured without encasing them with plastic. It’s essential to encase these components to make
Transparent plastic is being used in virtually every industry and this is because of its capacity to allow you see through and its ease of
Plastic is a common material used in the production of objects that can be used in homes, the automobile industry, and virtually all sectors. It
Basically, there are two kinds of plastics – thermoplastic, and thermosets. But the majorly talked about kind is the thermoplastic because of its versatile and
+86-755-8524 1121
marketing@rydtooling.com
No. 2, HongKan 1st Road, YanChuan Community, YanLuo Street, BaoAn District, ShenZhen City, China. Post Code 518105.
Subscribe to our newsletter to get manufacturing news and updates!