There are many technical terms related to the plastic injection process, understanding the vocabulary of plastic injection molding will help you improve your design for moldability and precision machining. Here are the terminology, terms, and definitions of the most important technicalities to comprehend while planning for the plastic injection molding process.
Injection Molding Terms and Definitions
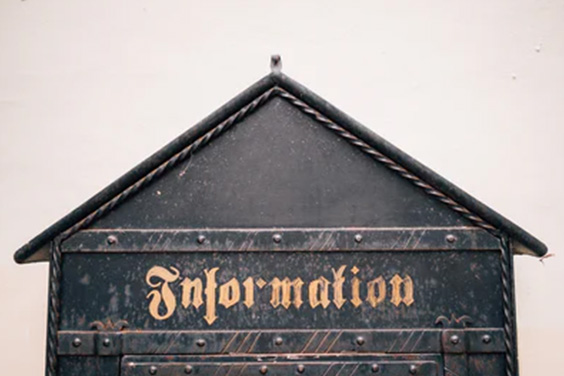
Additives
Additives are chemicals that are added to polymers to improve their overall functionality and appearance.
Alloy
A plastic alloy is a physical alteration of an existing plastic that results in improved performance and/or usefulness.
Annealing
This is the process of heating and slowly cooling a plastic item to allow the polymer chains to rebound and relieve internal tensions.
Assembly
Assembly is a secondary manufacturing operation that involves the connecting of completed pieces.
Backing Plate
A plate that sustains the injection tool’s mold, pins, and bearings.
Blister
As the name implies, this is a type of part defect that appears as a tiny bubble or blister on the surface of a component and is typically caused by gas or air bubbles.
Blow Molding
The method is similar to glass blowing in its fundamental phases. Air inflates a heated plastic mass. The plastic is pushed against the mold cavity by the air, forming the required shape. The plastic is expelled once it has cooled.
Bridge Tool
An injection mold that produces pieces while the final tool is being built. Such molds or tools aren’t intended to be used in operation.
Bubbles
These are bubbles developed within the plastic, comparable to blisters, gas pockets, or holes.
Cavity
The machining shape inside a mold that formed the shape of the plastic item is referred to as a cavity.
Clamp
The device secures the mold all through the injection molding.
Cold Slug
A defect is defined by a tiny non-uniform region on the component caused by an incorrectly hot piece of plastic adhering to the part.
Colorant
A pigment system, generally in the form of a pelletized, powdered, or liquid pigment, is combined with resin to generate the desired color.
Compression Molding
A heated plastic substance is squeezed into form after being put in a heated mold. The heating procedure, known as curing, ensures that the completed item retains its integrity.
Copolymer
A copolymer is a polymer composed of far more than just one monomer class.
Core
A core is an enlargement or group of appendages that form the inner surface of a plastic part. They are frequently regarded as the “masculine” half of the role.
Crazing
A flaw that creates tiny cracks in the plastic, usually caused by overstraining the material.
Creep
The “set” that a molded item undergoes when stressed and does not reshape back to its original form. Also referred to as “memory.”
Cure
The process of hardening or stabilizing a material.
Cycle
The whole amount of time required for the plastic injection process to manufacture a completed item.
Degassing
This is the process of opening and shutting a mold to enable gas to flow out. Parts with trapped gas or air can develop flaws such as scorching and bubbles.
Delamination
This defect shows on the component as a flaky outer surface and is frequently caused by contaminants or humidity in the resin pellets.
Density
A material’s quantity per unit volume.
Dimensional Stability
The capacity of a plastic item to keep its precise form after molding.
Draft
The inclination or level of taper of a sidewall to aid in component extraction from the mold.
EDM
Electric Discharge Machining, is a mold-making method in which the form of the mold cavity is produced by eliminating metal material utilizing electrical discharging.
Ejection Pins
These are metallic rods in the mold that push the components out.
Ejector Return Pins
Pins that restore the ejectors to their original position once the components have been freed.
Ejector Rods
Once the mold opens, an extraction rod contacts the ejector mechanism and pins.
Elasticity
A material’s capacity to return to its former condition after being stretched.
Elastomer
An extremely elastic rubber-like substance.
Extrusion
This is the technique of creating tubing or continuous forms by forcing molten material through a die opening.
Fabrication
The process of producing plastic items using various molding and shaping techniques.
Family Mold
A family mold is a mold that has cavities for multiple pieces.
Fan gate
A gate having a larger width that aids in the reduction of warping caused by stress.
Fill
The process of putting material into a mold.
Filler
An inert substance that increases a part’s strength or hardness.
Finish
A component’s surface texture.
Flash Gate
A variant of a fan gate is one where melted resins are conveyed through a narrower gate section, resulting in a continuous melt flow into the chamber.
Flash or Burrs
A narrow lip or protruding part beyond the surface of the component is caused by insufficient clamping force, inadequate mold design, and/or mold degradation.
Flow Marks
These are patterns or discolorations that appear as a result of slow injection speeds enabling fast cooling of the material.
Flow Rate
The amount of material that passes through a fixed location in a given amount of time.
Gate
A gate is a conduit via which molten plastic passes into a mold.
Hardness
An object’s tolerance for compression, deformation, and scratches.
Hot-Runner Molds
Hot-runner molds are made up of two panels that are heated using a manifold system. The molten plastic is directed by the manifold to pumps, which occupy the part voids.
Injection Blow molding
A blow molding method in which the blown part is produced by injection molding.
Injection Molding
This is a manufacturing technique that involves injecting molten plastic into a mold to produce a component.
Insert
An item that is introduced into the molded portion.
Jig
A device that holds and directs a tool throughout the manufacturing process.
Machine Shot Capacity
The amount of resin that can be sprayed in a single stroke on a device.
Masterbatch
A solid or liquid polymer addition is used for dyeing or imparting other characteristics to polymers.
Memory
The process through which plastic returns to its original size and shape.
Mold
A hollow shape into which plastic is injected or placed to create a plastic item.
Mold release
Surface treatment is used to help the component expel from the mold.
Multi-shot Molding
A method that involves injecting two or more plastic ingredients into a mold to produce a component. This method is frequently used in the production of toothbrushes.
Nozzle
The nozzle is a hollow-core metallic nose that is fitted into the injection end of the rod and creates a sealing under pressure.
Orange Peel
An uneven rough fault induced by mold cavity humidity or inadequate pack-out.
Over Molding
A two-shot technique in which two plastic materials are successively injected into a mold, often a tougher base material having a softer covering.
Parting Line
A line is produced on a part once the two ends of the mold meet.
Pinpoint Gate
An extremely tiny gate is used to regulate the flow of substances in hot runner molds.
Plastic
This is a high-molecular-weight polymeric material.
Plasticity
This is defined as the ability to be easily bent or molded.
Platens
Steel plates in the molding process hold the mold in place.
Polymer
A substance with a molecular structure is made up of a large number of similar units linked together, such as many synthetic organic compounds used as polymers and resins.
Prototype Tool
Also termed a soft tool, an early mold made to generate prototype components and used to make modifications to the final design tool.
Purging
The operation of cleansing the injection machine of residual color or substances before running a fresh component.
Ram
A plunger-like component that forces the molten metal into a mold.
Release Agent
A chemical that is deposited on the mold or cast into the component is an addition to aid in the extraction of the part.
Retainer Plate
A panel upon which the mold’s detachable components are attached.
Runner System
The channel structure that permits melted substances to flow into
component cavities.
Short Shot
A flaw in which the material does not fill the component cavity.
Shot
A whole injection tool cycle.
Shrinkage
The measure of volume loss occurs when a plastic substance cools.
Sprue
The entrance feed transports content from the nozzle towards the mold’s runner system.
Thermoplastic
A substance that can be continuously heated and cooled without altering its structure. Extremely recyclable.
Thermoset
A substance that can be crushed or molded into a form when heated. Because the temperature increase alters the structu
re of certain substances, they cannot be reheated.
Tie Bars
These are the bars that offer mechanical stability to the mold in the press. The tie bars allow the mold to open or close.
Toggle
A device that, as opposed to hydraulic clamping, is utilized to seal the mold manually
Tool
A mold is included in an injection machine to produce plastic components.
Undercut
A design defect causes depression or a bulge that prevents the item from being ejected from the mold. Undercuts are sometimes built into molds to guarantee that a part stays on the right side of the mold.
Vent
A tube from the workpiece that permits gas and air to escape when the resin is poured into the cavity, preventing various sorts of flaws.
Weld Line
Also known as a knit line, this is the point at which two flow formations meet and are unable to connect during injection molding.
The Bottom Line
You might have come across the aforementioned terminology before and did not know what any of the words meant. The article has been structured just for you to gain an understanding of the same so that when you plan to buy plastic injection molding, you do understand what it means to do so. On that note, we do recommend that you buy such products from a reputable injection molding OEM, that will ensure quality and international safety standards are met in your purchases.