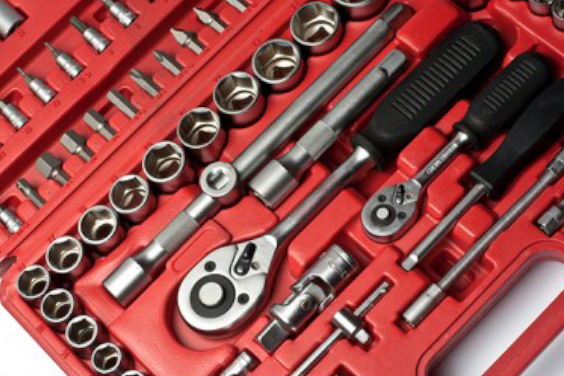
Insert Molding Process Step by Step
It is dangerous to make use of components after they’ve been manufactured without encasing them with plastic. It’s essential to encase these components to make
Share
Share
Plastic injection molding has been responsible for the creation of several plastic products, ranging from food containers to toys and plastic bottles. But then this has sparked your curiosity about the very equipment responsible for this work. Well, you have come to the right place. This article aims to inform you of plastic injection molding machines, detailing the various types and the advantage that each of these brings to the manufacturing process.
China plastic injection mold is very significant in the world of plastic products for many primary motivations, the most prevalent of which is that it is the best way to produce immense and comparable quantities of plastic parts.
Injection molding machines are divided into two parts: an injection unit and a clamping unit. It appears simple enough until you consider the end user’s diverse requirements. Various industries, and different functions, necessitate a wide range of machines.
Molding machines come in a variety of shapes and sizes, depending on what you’re doing and how the machine influences the result. Machines are classed mostly based on the type of drive system they employ: hydraulic, electric, or hybrid.
Source: Pinterest
Traditionally, hydraulic processes were the only option offered to molders until 1983, when a Japanese company launched the first all-electric injection molding machine. Hydraulic machines, while not as precise, are the most common in most of the world, except for Japan. A robotic arm is frequently used to extract the molded parts, either from the side or from the top, but parts are more commonly dropped out of the mold, via a chute, and into a vessel.
These hydraulic injection molding machines offer a variety of advantages to the manufacturer;
Lower starting price: These systems are considerably less expensive than their competitors.
Lower cost parts: If a machine part needs replacing resulting from damage or the part’s lifespan has expired, the spare parts are less expensive and easier to manage.
Tougher parts: The tool’s hydraulic components are more durable and strong and resistant to damage ensuring they are built to last.
Hydraulic injection molding machines have a high clamping force.
Source: Pinterest
As previously stated, electric molding machines only became applicable in the 1980s and quickly gained popularity. They are ideal for short injection times and will provide the highest level of production sanitation. Electric injection molding machines, also recognized as motor technology (EMT), reduce operating costs by lowering energy consumption while also addressing some environmental concerns associated with hydraulic presses.
Here are a few advantages of using an all-electric injection molding machine:
Efficiencies: Electric injection molding machines only use power when they are in use, which means that the engine output is limited to the peak load.
There is no risk of oil leakage, so there is less downtime. Furthermore, the absence of oil means that no filters must be replaced, resulting in lower consumable costs.
Faster process: Because these machines are digitally monitored, the system is repeatable and does not require supervision.
Clean operation: Because this machine does not use oil, it is suitable for manufacturing medical parts. Typically, these parts should be made in a clean-room environment.
Source: Pinterest
Hybrid injection molding machines appear to be taking advantage of key functionalities of both the hydraulic and electric machines, but in reality, depending on the make, use roughly the same electricity consumption to continue operating as an electric injection molding machine.
To some, hybrid models assure the best outcome by combining the advantages of an electric motor and hydraulics. The following are some of the advantages of a hybrid injection molding machine:
Diversification: the various hybrid injection molding machine configurations allow for new levels of versatility.
Hybrid molding machines integrate the energy efficiency and precision of electric molders mostly with the force-generating capability of a hydraulic unit to provide the best of both worlds.
Motor replacement: Hybrids have substituted fixed-speed DC pump motors with fluctuating AC drives, allowing the pump to function only when needed and use the minimum amount of oil for efficiency.
Less outage: Compared to all-hydraulic or all-electric molding machines, these require minimal maintenance and have fewer outages.
Source: Pinterest
The switch system is used on mechanical-type machines to ramp up tonnage on the clamp side of the device. Tonnage is needed on all hardware so that the injection pressure doesn’t cause the tightening side of the machine to access. If the tool only partially opens, it will cause a flash in the plastic product.
Mechanical injection molding machines have an ideal balance of stability and performance as a result of system architecture and productivity matrices. These machines are built with the Hydro-Mechanical concept in mind. Mechanical injection molding machines have qualities such as strong performance, low oil consumption, more daylight, higher energy efficiency, and high productivity.
Plastic injection molding machines are by far one of the most adaptable equipment when it relates to plastics design tools, responsible for roughly 75 percent of primary plastics machinery. These extremely valuable machines could be used to create almost anything for plastic injection OEM, from tiny hearing aid components to large individual components such as tractor hoods.
When trying to define the perks of each injection molding machine, the principal feature required for that specific molding process and the subsequent product being generated is referred to. Contracting a plastic injection mold toolmaker & molding services in china not only offers a financially viable option but also one of the best quality services available worldwide.
It is dangerous to make use of components after they’ve been manufactured without encasing them with plastic. It’s essential to encase these components to make
Transparent plastic is being used in virtually every industry and this is because of its capacity to allow you see through and its ease of
Plastic is a common material used in the production of objects that can be used in homes, the automobile industry, and virtually all sectors. It
Basically, there are two kinds of plastics – thermoplastic, and thermosets. But the majorly talked about kind is the thermoplastic because of its versatile and
+86-755-8524 1121
marketing@rydtooling.com
No. 2, HongKan 1st Road, YanChuan Community, YanLuo Street, BaoAn District, ShenZhen City, China. Post Code 518105.
Subscribe to our newsletter to get manufacturing news and updates!